Copper sheets and strips for buildings
Copper sheets and strips for buildings(Mitsubishi Shindoh)
Standard: Copper sheet. JIS H3100 Phosphorous-deoxidized copper plate. (DCUP). C1220P-1/4H or 1/2H, Copper strip. JIS H3100. Phosphorous-deoxidized copper strip. (DCUR) C1220R-1/2H
Producer: Mitsubishi Materials Corporation
Certificate of incombustibility: Approved by Minister of Land, Infrastructure and Transport. NM-8595
Wide copper strip (Europe)
Standard: Wide copper sheet. Standard: Copper strip. equivalent to JIS H3100. Phosphorous-deoxidized copper strip. Thickness: 0.3mm/0.35mm/0.4mm/0.5mm. Width: 1000mm
Country of origin: Europe
Properties of copper sheets/strips for buildings
Copper sheets are of oxygen-free, tough-pitch, or phosphorous-deoxidized varieties. Phosphorous-deoxidized sheets are used for roofing metal. Phosphorous-deoxidized copper is smelted using phosphorous so a miniscule amount of phosphorous remains. It is the best kind for bending and welding
Physical properties
The chart below compares the physical properties of metals used in roofs. It is important to distinguish the metals and their properties according to intended assembly and usage. With metals, a particular problem is their flexibility due to heat expansion. Copper is 1.4 times more flexible than iron, making it more or less the same as stainless steel, and is 70% as flexible as aluminum. In the height of summer the surface temperature of copper sheets reaches 80℃ making a difference of 90-100℃ with its winter temperatures. The heat expansion based on this temperature difference is 100 x 1.7 = 170mm. For example, a single batten seam of 100m will expand and contract by 170mm. The longest piece of copper plating is fixed at 6m and between 5-6m expansion is taken for this size variance for tiling.
According to Young’s modulus, which is the standard for stretching and bending, copper comes in at 60% of lead making it a fairly soft metal. While this makes it easy to work on, it also leads to change in its shape due to expansion and contraction and external force. It is 3/4 as hard as iron and half as hard as stainless steal meaning the surface can be damaged during assembly – care must be taken during any work performed on the metal.
|
|||||||||
Property | Copper | Aluminum | Zinc | SUS304 | |||||
Relative density | 8.94 | 2.70 | 7.86 | 7.93 | |||||
Linear rate of expansion (mm/100m/℃) | 1.7 | 2.4 | 1.2 | 1.7 | |||||
Rate of heat conduction (W/m・℃) | 385 | 138 | 54 | 16 | |||||
Specific heat (J/g・℃) | 0.38 | 0.96 | 0.48 | 0.5 | |||||
Yield point (N/㎟) | 137 | 216 | 264 | 235 | |||||
Young’s modulus(104N/㎟)) | 12 | 7 | 21 | 20 | |||||
Tensile strength (N/㎟) | 245 | 245 | 343 | 588 | |||||
Shear resistance(N/㎟) |
196 |
98 |
294 |
490 |
|||||
Hardness(Hv) | 75 | 75 | 100 | 150 |
Chemical properties
Chemical properties of copper
The extent of discoloring of copper
Before work is performed on them, copper sheets have a reddish-orange color, but upon contact with the atmosphere, this turns brownish due to cuprous oxide and oxidized copper forming and this color gradually becomes darker. When it rains after any work the color changes easily and the color of the extremely thin film formed on the surface is affected. This means that the composition of the copper may be questionable and there may be unusual oxidation. This an ageing process and generally the change in color will settle down after 3-6 months. After this, a green color gradually starts to appear due to the effects of rain and the environment. Eventually, after many years, basic (i.e. not acidic) carbonate and basic copper chloride are compositely formed and this becomes a delicate protective film. Oxidized copper has different colors depending on its variety and the oxidized form differs depending on the environment and surroundings and the slope and positioning of the roof. Thus, the same roof differs in parts and is not even. Not all copper plates have the same color changes and the natural environment and the condition of the building largely control the change. Below are the typical color changes.
Reddish orange – brown – dark brown – blackish brown – blue-greenTime of assembly
Twenty years later
The chart below shows copper’s resistance to chemicals. Copper is weak to ammonia and ammonia compounds, sulfur, hydrogen sulfide and mercury, and is drenched by nitric acid and concentrated nitric acid. The risk of corrosion is greatly increased in hot spring areas with hydrogen sulfide and sulfur gas and near smoke-producing facilities that burn heavy fuel containing sulfides at high temperatures.
Chemical resistance of copper | |||||
Item |
Corrosion |
Item |
Corrosion |
Item |
Corrosion |
Alcohol |
A |
Mercury |
D |
Sulfur (dry) |
B |
Ammonia (wet) |
D |
Natural gas |
B |
Sulfur (soluble) |
D |
Ammonium hydroxide |
D |
Nitric acid |
D |
Sulfur dioxide (wet) |
B |
Ammonium chloride |
D |
Nitrogen |
A |
Sulfuric acid |
B |
Ammonium nitrate | C | Oxygen | A | Sulfurous acid | B |
Ammonium sulfate | C | Sea water | B | Tar | A |
Carbonated water | B | Sewage | A | Varnish | A |
Carbon Dioxide | B | Soapy water | A | Drinking water | A |
Chlorine | C | Sodium chloride | B | Factory conditions | A |
Hydrogen | A | Water vapor | A | Sea water conditions | A |
Hydrogen sulfide (wet) | D | Vinegar | B | Rural conditions | A |
A: Complete resistance – no corrosion. B: Can be used with no problem, under partial conditions. C: Can be used in partial conditions but is corroded. D: Inappropriate for use
When it rains on copper roofs, the copper is partly ionized and this copper ion dissolves in the rain water. When this copper ion comes into contact with concrete or mortar, these alkalis react and become copper hydroxide and dye the mortar and concrete green. If the ions fall onto rocks they absorb carbonic gas, become copper carbonates and dye the rock green. It is important to take precautions on the external walls and under the eaves of the building if roof bypasses gutters and falls directly to the ground,
Electric corrosion
The chart shows metals in order of electric potential . As is shown below, the electric potential between copper and stainless steel is small and there is no electric corrosion. In recent years, the nails used in copper roofs have mostly been made of stainless steel.
Galvanic series | |
+
- |
US316 Stainless steel SUS304 Stainless steel Monel metal Nickel Copper Aluminum bronze Bronze Tin Lead Tin solder Cast iron Soft iron Aluminum compound 2014 Aluminum compound 2017 Cadmium Aluminum compound 5052 Zinc-coated steel Zinc Magnesium
|
Reference: Nihon Shindoh Cooperation. Shindoh product data book
Durability of copper sheets
Holes opening in copper sheets
Photo1
It has been told for many years that holes appear in copper sheets when they corrode in acid rain. However, this phenomenon is limited to copper gutters on tiled roofs and parts where tiles and copper sheets touch in thatched-style roofs. It is thought that the reason for this is not inly rainwater concentrated in the center of tiles but also a height difference; the oxidized film that forms is detached and a new film is not formed (erosion). (Refer to photo 1) Further, there is thought to be a large effect caused by elution from the tiles and glazes. If this copper corrosion is due to acid rain, roofs made of straight slating with whole copper sheets should also have holes. Photo 2 is of the rooftop structure of the copper sheet roof of the central public hall in Osaka, renewed in 2002. The roof is 80 years old, having been laid in 1918 with a thickness of 0.35mm. It is surrounded by stable natural greenery and was not corroded at all. Thus, roofs entirely made of copper sheets do not undergo this hole-opening phenomenon. Based on this, it is thought that corrosion is due to usage rather than acid rain. Preventive measures for this include double-layered sheets where they touch tiles and assembly methods that increase the thickness of the sheets. Photo 2
Example of thatched-style roofing
Durability of copper roofing against acid rain.
Reduction in copper / (48 places around the world: 4 year average for 1986-89)
Reduction in copper / (48 places around the world: 4 year average for 1986-89) |
|
Tokyo |
0.0006㎜/year |
Places with concentrated sulfuric acid (3-14 times that of Tokyo) |
0.0014~0.0033㎜/year |
Reduction in copper / (48 places around the world: 4 year average for 1986-89) |
|
Okinawa | 0.0023㎜/year |
Places with concentrated chlorine (2-6 times that of Tokyo) | 0.0017~0.0031㎜/year |
Taken from the Japan Copper Centre data
Copper sulfide sheets
Copper sulfide sheets
Copper sulfide
example assembly
Copper sulfide sheets, standards chart | ||
Thickness(mm) | Width(mm) | Length(mm) |
0.30 |
365 | 1212 |
455 | 1212 | |
0.35 |
365 | 1212 |
455 | 1212 | |
606 | 1212 | |
0.40 | 365 | 1212 |
455 | 1212 | |
606 | 1212 | |
0.50 | 365 | 1212 |
455 | 1212 |
Note 1: All copper sulfide sheets are made on commission.
Note 2: Copper sulfide sheets may have a certain amount of color spotting due to their coloring being chemical; this spotting will become less conspicuous over time.
Note 3: Due to the nature of the surface film of copper sulfide sheets, the film may separate from the part that is worked on when bending the sheets. This filmless part will become less conspicuous over time.
Stock list
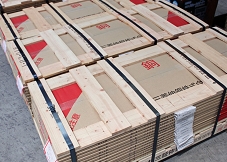
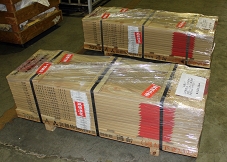
Stock list of copper sheets for buildings | |||
Thickness (mm) | Size (mm) | Weight (kg/sheet) | Sheets/package |
0.25 | 365x1212 | 1.00 | 40 |
0.30 | 365x1212 | 1.20 | 40 |
455x1212 | 1.49 | 30 | |
0.35 | 365x1212 | 1.39 | 30 |
455x1212 | 1.74 | 30 | |
606x1212 | 2.29 | 15 | |
0.40 | 365x1212 | 1.59 | 30 |
455x1212 | 1.99 | 20 | |
606x1212 | 2.62 | 15 | |
1000x2000 | 7.20 | ||
0.50 | 365x1212 | 1.99 | 20 |
455x1212 | 2.48 | 20 | |
1000x2000 | 9.00 |
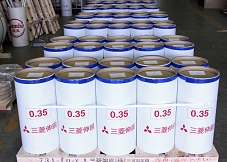
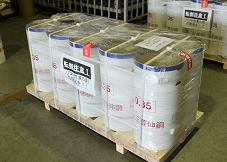
Stock list of copper strips for building | |||
Width(mm) | Thickness(mm) | Length(mm) | Enacted weight (kg) |
182 | 0.30 | ||
0.35 | |||
0.40 | |||
227 |
0.30 | ||
0.35 | |||
0.40 | |||
303 | 0.30 | 60 | 48.6 |
0.35 | 50 | 47.3 | |
0.40 | 45 | 48.6 | |
305 | 0.30 | ||
0.35 | |||
0.40 | |||
365 | 0.30 | 50 | 48.8 |
0.35 | 40 | 45.6 | |
0.40 | 35 | 45.6 | |
0.50 | |||
455 | 0.25 | ||
0.30 | 40 | 48.7 | |
0.35 | 35 | 49.7 | |
0.40 | 30 | 48.8 | |
0.50 | |||
500 | 0.30 | ||
0.35 | |||
0.40 | |||
606 | 0.30 | 30 | 48.7 |
0.35 | 25 | 47.4 | |
0.40 | 20 | 43.4 | |
1000 | 0.30 | 20 | |
0.35 | 20 | ||
0.40 | 20 | ||
0.50 | 15 |
We may be missing the item of stock list. There also may be unforeseen changes to the content – we apologize for any inconvenience.
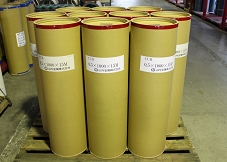
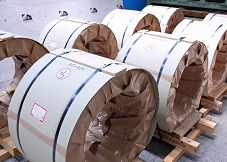